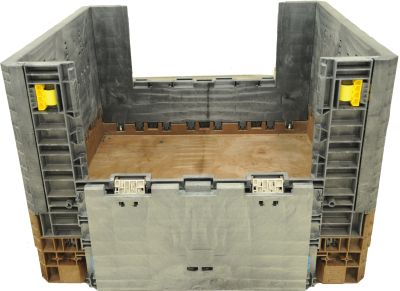
This is the third and final article in a three-part series. The first article defined reusable transport packaging and its role in the supply chain, the second article detailed the economic and environmental benefits of reusable transport packaging, and this last article supplies some parameters and tools to help readers determine whether it is beneficial to change all or some of a company’s one-time or limited-use transport packaging to a reusable transport packaging system.
When considering implementing a reusable transport packaging system, organizations must take a holistic view of both economic and environmental systems costs to measure the potential overall impact. In the operating expense reduction category, there are several areas where cost savings plays a key role in evaluating whether or not reuse is an attractive option. These include material substitution comparisons (single-use versus multi-use), labor savings, transportation savings, product damage issues, ergonomic/worker safety issues and a few other major savings areas.
In general, several factors determine whether it would be beneficial to change all or some of a company’s one-time or limited-use transport packaging to a reusable transport packaging system, including:
A closed-or managed open-loop shipping system: Once reusable transport packaging is shipped to its final destination and contents are removed, the empty transport packaging components are collected, staged, and returned without a great deal of time and cost. Reverse logistics—or the return trip for empty packaging components—must be repeated in a closed-or managed open-loop shipping system.
A flow of consistent products in large volumes: A reusable transport packaging system is easier to justify, maintain, and run if there is a flow of consistent products in large volumes. If few products are shipped, the possible cost savings of reusable transport packaging may be offset by the time and expense of tracking empty packaging components and reverse logistics. Significant fluctuations in shipping frequency or types of products shipped may make it difficult to accurately plan for the correct number, size, and type of transport packaging components.
Large or bulky products or those easily damaged: These are good candidates for reusable transport packaging. Larger products require bigger, more expensive one-time or limited-use containers, so the potential for long-term cost savings by switching to reusable transport packaging is great.
Suppliers or customers grouped near one another: These make likely candidates for reusable transport packaging cost savings. The potential to set up “milk runs” (small, daily truck routes) and consolidation centers (loading docks used to sort, clean, and stage reusable transport packaging components) creates significant cost-saving opportunities.
Inbound freight can be picked up and consolidated for delivery on a more frequent just-in-time basis.
In addition, there are some key drivers that lend themselves to higher levels of reuse adoption, including:
· High volumes of solid waste
· Frequent shrinkage or product damage
· Expensive expendable packaging or recurring single-use packaging costs
· Underutilized trailer space in transportation
· Inefficient storage/warehouse space
· Worker safety or ergonomic issues
· Significant need for cleanliness/hygiene
· Need for unitization
· Frequent trips
Generally, a company should consider switching to reusable transport packaging when it would be less expensive than one-time or limited-use transport packaging, and when it is striving to reach sustainability goals set for their organization. The following six steps will help companies determine if reusable transport packaging can add profit to their bottom line.
1. Identify potential products
Develop a list of products frequently shipped in large volume and/or that are consistent in type, size, shape and weight.
2. Estimate one-time and limited-use packaging costs
Estimate current costs of using one-time and limited-use pallets and boxes. Include costs to purchase, store, handle and dispose of the packaging and added costs of any ergonomic and worker safety limitations.
3. Develop a geographical report
Develop a geographical report by identifying shipping and delivery points. Evaluate the use of daily and weekly “milk runs” and consolidation centers (loading docks used to sort, clean and stage reusable packaging components). Also consider the supply chain; it may be possible to facilitate a move to reusables with suppliers.
4. Review reusable transport packaging options and costs
Review the various types of reusable transport packaging systems available and the costs to move them through the supply chain. Investigate the cost and life span (number of reuse cycles) of reusable transport packaging components.
5. Estimate the cost of reverse logistics
Based on the shipping and delivery points identified in the geographical report developed in Step 3, estimate the cost of reverse logistics in a closed-loop or managed open-loop shipping system.
If a company chooses not to dedicate its own resources to managing reverse logistics, it can obtain the assistance of a third-party pooling management company to handle all or part of the reverse logistics process.
6. Develop a preliminary cost comparison
Based on the information gathered in the previous steps, develop a preliminary cost comparison between one-time or limited-use and reusable transport packaging. This includes comparing the current costs identified in Step 2 to the sum of the following:
– The cost for the amount and type of reusable transport packaging researched in Step 4
– The estimated cost of reverse logistics from Step 5.
In addition to these quantifiable savings, reusable packaging has been proven to reduce costs in other ways, including reducing product damage caused by faulty containers, reducing labor costs and injuries, reducing space required for inventory, and increasing productivity.
Whether your drivers are economic or environmental, there is a strong likelihood that incorporating reusable packaging in your supply chain will have a positive impact on your company’s bottom line as well as the environment.
Post time: May-10-2021